You Might Be the Reason Your Staff are Making Mistakes
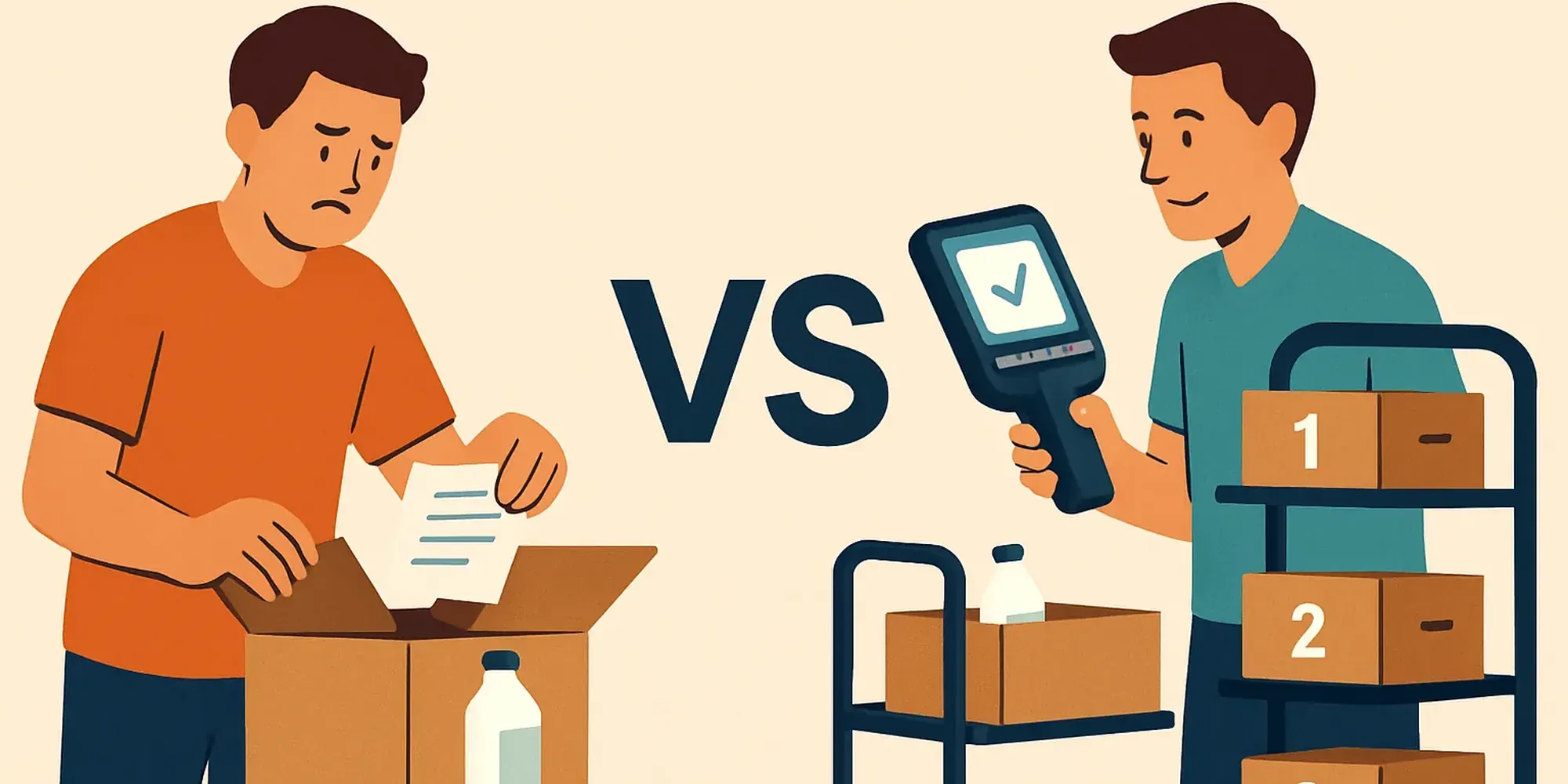
Most business owners and ops managers don’t realise it…
But the biggest limitation in your business isn’t your team, your tools, or your margins.
It’s human capacity — and the way you’re using it.
Let’s break it down with a real-world example that happens every day in food, retail, and manufacturing.
The Manual Pick & Pack Trap
Pick and pack seems simple — until you scale.
Most businesses run a fully manual process:
- A team member prints a picking slip
- They walk the floor trying to find each item
- They mentally cross-check quantities
- They pack it, hoping nothing’s missed
This might work when you're doing a handful of orders. But as volume grows, so do mistakes — and stress.
Every manual pick requires critical thinking:
- Is this the right product?
- Right size or variant?
- Did I pick the right amount?
- Where even is this bin?
The average person can only focus like that for about 4 hours a day.
So even on a good day, that’s:
- 24 orders max (if each takes ~10 minutes)
- A couple of mistakes
- And rising risk of burnout over time
Scaling Without Burnout: Use Supply’d Pick & Pack
Now let’s look at how it works with Supply’d’s scanner-based Pick & Pack:
- Your team member sets up a cluster pick using numbered tubs on a trolley
- They’re guided step-by-step through the floor, with bin locations for each item
- Each product shows a clear image for visual confirmation
- They scan the item using a touchscreen barcode scanner
- If the wrong product or qty is scanned, the system flags it instantly
No second-guessing. No memory games. No paperwork.
Now you’re getting:
- 7-minute average per order - probably even faster depending on your warehouse size
- Up to 64 orders picked & packed per day, per picker
- Consistent accuracy
- Happier team members who can stay in the zone longer
You're not just getting more done — you're creating a better work environment.
The Bottleneck Isn’t Your Team — It’s the Process
If you’re still relying on paper slips, checklists, or memory to pick orders — you're building inefficiency into your operations.
And when the only way to scale is “hire more people and hope they don’t burn out,” something's got to change.
Multiply the Impact Across Your Whole Business
The same logic applies beyond pick and pack.
Everywhere your team is forced to rely on memory, guesswork, or repeated double-checking — you're losing time and bleeding margin.
- Recipe management
- Purchase ordering
- Price syncing
- Delivery planning
- Batch tracking
- Expense processing
- Stock transfers
This is where tech like Supply’d doesn’t just make your job easier — it unlocks your team's potential.
Bottom Line
Your staff aren’t the issue.
Your growth isn’t the issue.
But if you’re still making people think through tasks that Supply’d can automate, guide, or validate — you might be the bottleneck.
And that’s good news.
Because it means you can fix it — fast.